¿Qué es el calentamiento por inducción?
El calentamiento por inducción se basa en el suministro de energía mediante inducción electromagnética.
Una bobina, adecuadamente dimensionada y colocada cerca de las piezas metálicas a calentar, atravesada por corriente alterna de alta o media frecuencia, induce en la pieza de trabajo corrientes (corrientes de Foucault) cuya intensidad puede ser controlada y modulada.
El calentamiento se produce sin contacto físico, afecta solo a las piezas metálicas a tratar y se caracteriza por una transferencia energética altamente eficiente sin pérdida de calor.
La profundidad de penetración de las corrientes generadas está directamente relacionada con la frecuencia de trabajo del generador utilizado; cuanto mayor es la frecuencia, más se concentran las corrientes en la superficie. En este caso, la homogeneidad del calentamiento en una masa importante puede lograrse gracias al principio de conducción térmica, que permite que el calor se propague en profundidad.
Principales Aplicaciones del Calentamiento por Inducción
- Soldadura fuerte
- Soldadura con estaño
- Tratamientos térmicos (templado, recocido, revenido, etc.)
- Fusión (metales ferrosos y no ferrosos)
- Forja
- Ajuste por contracción
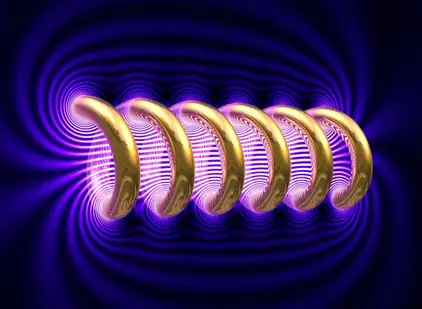
Beneficios y Ventajas del Calentamiento por Inducción
El calentamiento por inducción se aplica ampliamente en aplicaciones industriales y permite obtener:
- Reducción del tiempo de calentamiento
- Calentamiento localizado
- Consumo energético eficiente
- Proceso de calentamiento controlable y repetible
- Mejora de la calidad del producto
- Seguridad para el usuario
- Mejora de las condiciones laborales
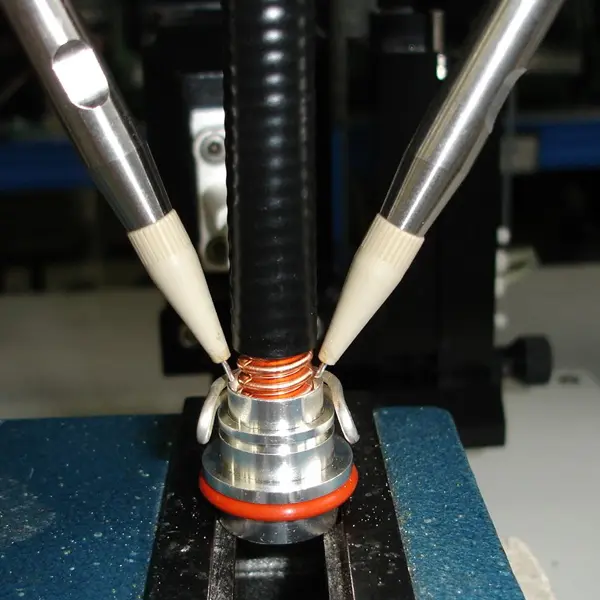
¿Cómo funciona el calentamiento por inducción?
El fenómeno del calentamiento por inducción electromagnética se basa en tres principios físicos, que se explican a continuación:
- Transferencia de energía del inductor a la pieza a calentar mediante campos electromagnéticos.
- Transformación de la energía eléctrica en calor por efecto Joule. (P=I²R)
- Transmisión del calor dentro de la masa mediante conducción térmica.
El campo electromagnético es generado por la corriente que circula por la bobina.
Si la bobina tiene forma de solenoide, la intensidad del campo electromagnético también es proporcional al número de vueltas.
Una pieza colocada dentro o cerca de la bobina de calentamiento experimenta corrientes parásitas, también llamadas corrientes de Foucault.
Según la ley de Laplace, la intensidad del campo magnético es inversamente proporcional al cuadrado de la distancia desde la bobina.
Según la ley de Faraday-Lenz, la corriente inducida en la pieza es proporcional a la velocidad de cambio del flujo magnético (frecuencia).
Las corrientes de Foucault son corrientes inducidas en conductores que se oponen al cambio del flujo que las generó. Aparecen cuando un conductor es expuesto a un campo magnético cambiante.
Estas corrientes circulares crean campos magnéticos inducidos que se oponen al cambio del campo magnético original según la ley de Lenz, causando fuerzas de repulsión o arrastre entre el conductor y la bobina.
Cuanto más fuerte sea el campo magnético aplicado, o mayor sea la conductividad eléctrica del conductor, o más rápida sea la variación del campo, mayor será la corriente generada.
La energía inducida en la pieza a calentar depende de:
- Intensidad de la corriente en la bobina
- Frecuencia de operación
- Forma de la bobina y distancia a la pieza
- Permeabilidad magnética y resistividad de la pieza (influidas por la temperatura objetivo y la temperatura de Curie en materiales magnéticos)

Efecto pelicular
El efecto pelicular es la tendencia de una corriente eléctrica alterna (AC) a distribuirse dentro de un conductor con una mayor densidad de corriente cerca de la superficie y disminuyendo con la profundidad. El efecto pelicular se debe a corrientes parásitas opuestas inducidas por el campo magnético variable generado por la corriente alterna. Por lo tanto, cuanto mayor sea la frecuencia de trabajo, más se concentrará el calentamiento por inducción en la superficie externa de la pieza.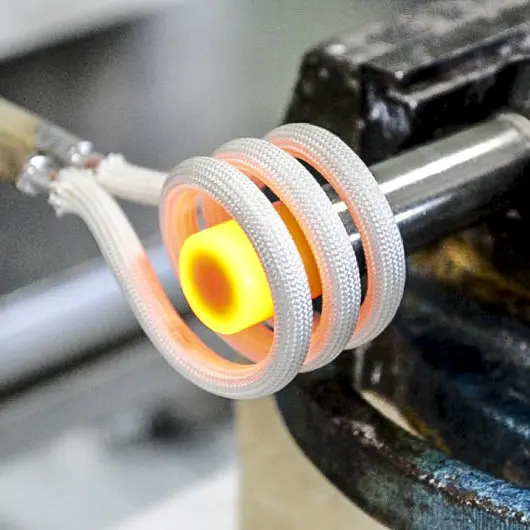
Bobina de calentamiento por inducción
Se utiliza para transferir energía a la pieza. El diseño de la bobina es uno de los elementos más importantes del sistema y representa una ciencia en sí misma. La bobina está diseñada para:
- concentrar el calentamiento solo donde sea necesario
- maximizar la eficiencia del calentamiento
- permitir la integración en la máquina de producción
Estructura e historia de los generadores de calentamiento por inducción
Un calentador por inducción normalmente consta de tres elementos
- Unidad de potencia (inversor/generador): Esta parte del sistema se utiliza para tomar la frecuencia de la red y aumentarla a un rango entre 20 y 900 kHz. La potencia de salida típica de una unidad es de 2 a 500 kW.
- Cabezal de trabajo: Contiene una combinación de condensadores y transformadores y se usa para adaptar la unidad de potencia a la bobina de trabajo
- Bobina de trabajo (inductor): Se usa para transferir energía a la pieza. El diseño de la bobina es uno de los elementos más importantes del sistema y es una ciencia en sí misma
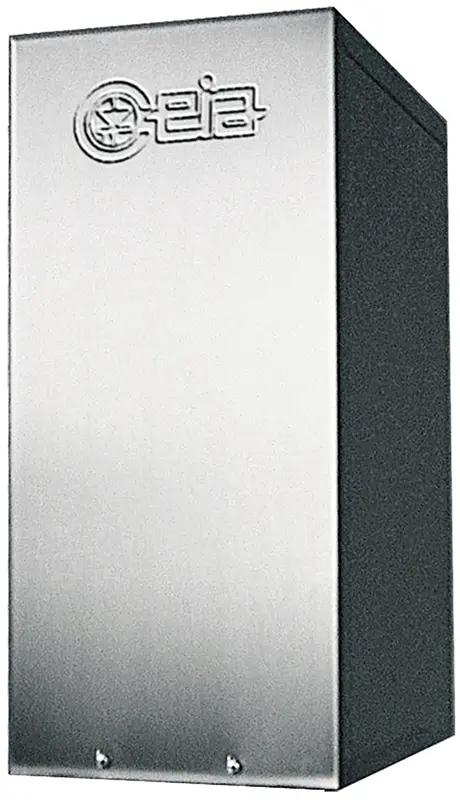
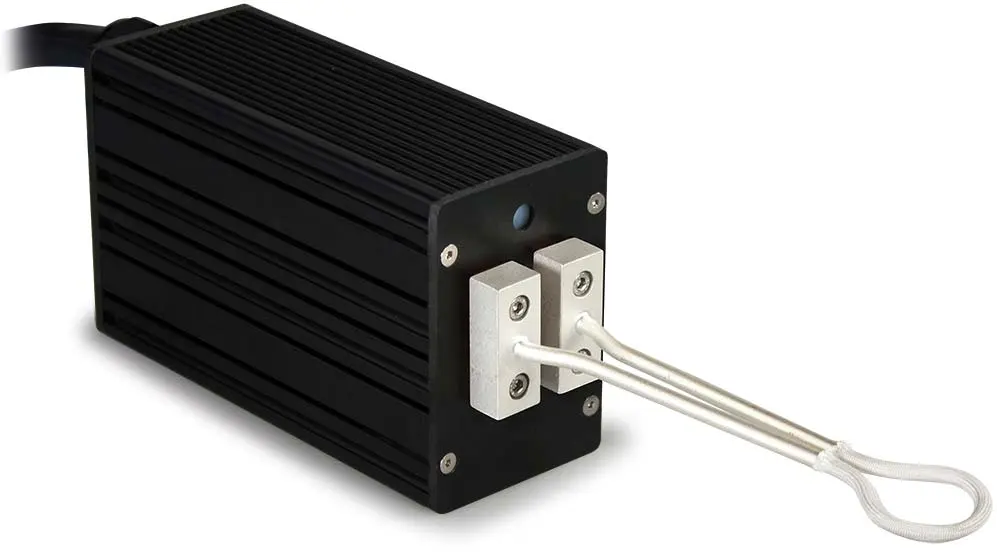
Estructura clásica - Generador oscilador de válvulas (1970-1990)
La tríodo termoiónica de vacío con múltiples electrodos (válvula) era el corazón del circuito auto-oscilante responsable de crear la corriente eléctrica de alta frecuencia que circula por la bobina.
Problemas:
- Inestabilidad de la potencia de salida: la potencia de salida se ve afectada por las fluctuaciones del voltaje de alimentación, y el generador no puede seguir la potencia establecida en caso de variación de carga (por ejemplo, calentamiento por encima del Punto de Curie)
- Difícil regulación de potencia
- Baja eficiencia (casi 60 %)
- Vida útil de la válvula
- Muy alto voltaje anódico (peligro para la seguridad del operador)
- Grandes dimensiones totales
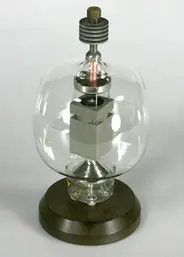
Estructura convencional (1990 – hoy) - Generadores de transistores de estado sólido
Hoy en día, el uso de transistores MOSFET o IGBT ha reemplazado el uso de válvulas de vacío y se ha convertido en el corazón de todos los generadores inductivos convencionales en el mercado.
Características principales:
- Dimensiones generales más pequeñas que los generadores con válvulas
- Mayor eficiencia
- Rango de frecuencia de trabajo más alto
Problemas:
- Alto flujo de corriente desde el generador a la cabeza de calentamiento
- Inestabilidad de la potencia de salida en caso de fluctuaciones del voltaje de la red o variaciones de carga
- El uso del generador convencional es posible solo en procesos de calentamiento con amplias tolerancias permitidas.
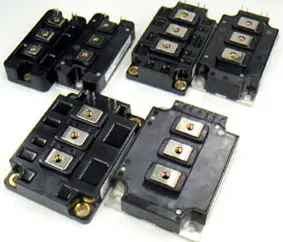
Generadores de calentamiento por inducción CEIA
Principales características y diferencias respecto a los generadores convencionales
- Control en tiempo real de la generación de potencia mediante microprocesador
- Diseño extremadamente compacto
- Sensores de retroalimentación de voltaje de la bobina
- Cabezal de calentamiento resonante (bajo flujo de corriente del generador al cabezal de calentamiento)
- Mantiene una potencia de salida estable incluso cuando cambian las condiciones de trabajo (informe de calibración)
- Unidad de control específica para el control de potencia de salida
- Certificaciones EMC y CE
Bucle de control preciso mediante retroalimentación de:
- Voltaje de la bobina
- Corriente de la bobina
- Fase de salida RF
- Corriente de entrada
- Pirómetro óptico para control de temperatura (80÷2200 °C) (175÷3990 °F)
Un total de 5 parámetros de retroalimentación para asegurar un proceso de calentamiento preciso y constante.
El sistema de calentamiento inductivo CEIA permite un control de temperatura muy rápido y preciso. Son adecuados para procesos industriales y automáticos, y también se instalan en sistemas robóticos donde se requiere:
- Repetibilidad extremadamente alta
- No se admiten tolerancias
Prueba gratuita de muestras
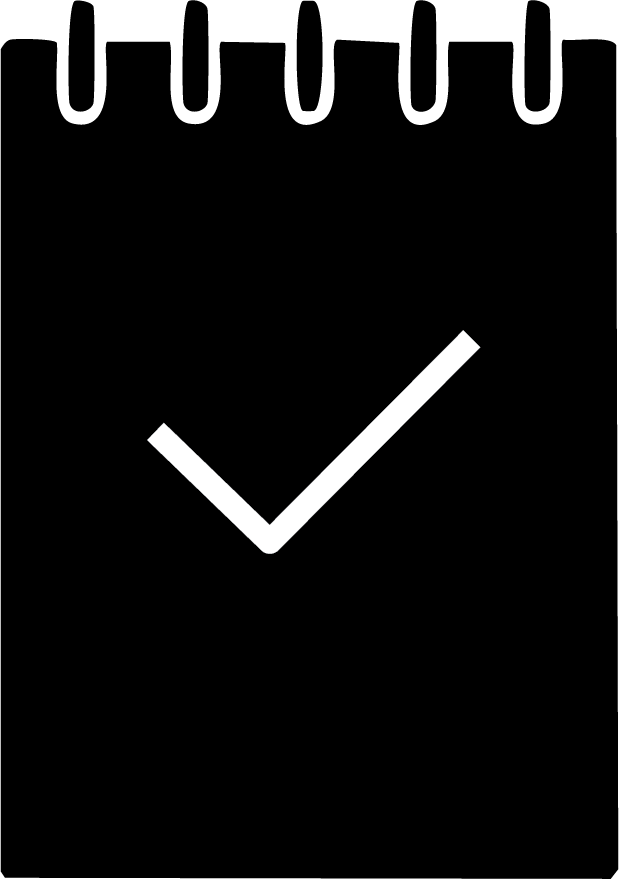
Cotizaciones rápidas
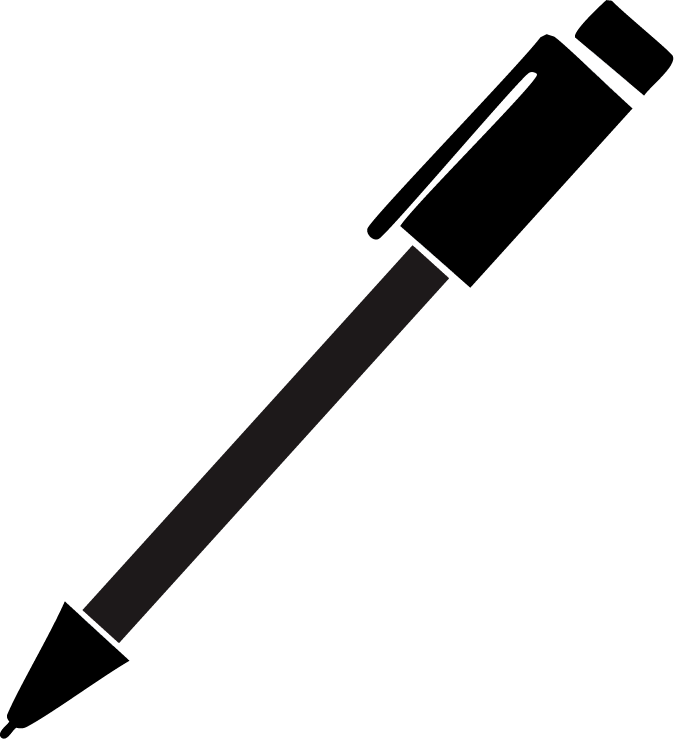