Draht- und Kabelproduktion
Der Bereich der Draht- und Kabelherstellung ist für die Herstellung von elektrischen, Datenübertragungs- und Strukturleitern verantwortlich, die hauptsächlich aus Kupfer, Aluminium und Speziallegierungen bestehen. Diese Produkte sind grundlegende Komponenten für verschiedene Anwendungen, einschließlich der elektrischen Energieverteilung, Telekommunikationsnetzen, Automobilsystemen, Luft- und Raumfahrtplattformen, elektronischen Geräten und Bauprojekten. Ein zentraler Schwerpunkt liegt auf der Optimierung der elektrischen Leitfähigkeit, der mechanischen Flexibilität, der strukturellen Haltbarkeit und, entscheidend, der Aufrechterhaltung der Isolationsintegrität und einer überlegenen Oberflächenqualität.
Die Fertigungsprozesse innerhalb dieser Industrie erfordern Hochgeschwindigkeits-, kontinuierliche Produktionsmethoden, gekoppelt mit einer strengen Kontrolle sowohl der physikalischen als auch der elektrischen Eigenschaften. Folglich stellt die Induktionserwärmung eine optimale Lösung für zahlreiche kritische Phasen innerhalb dieses Fertigungsablaufs dar.
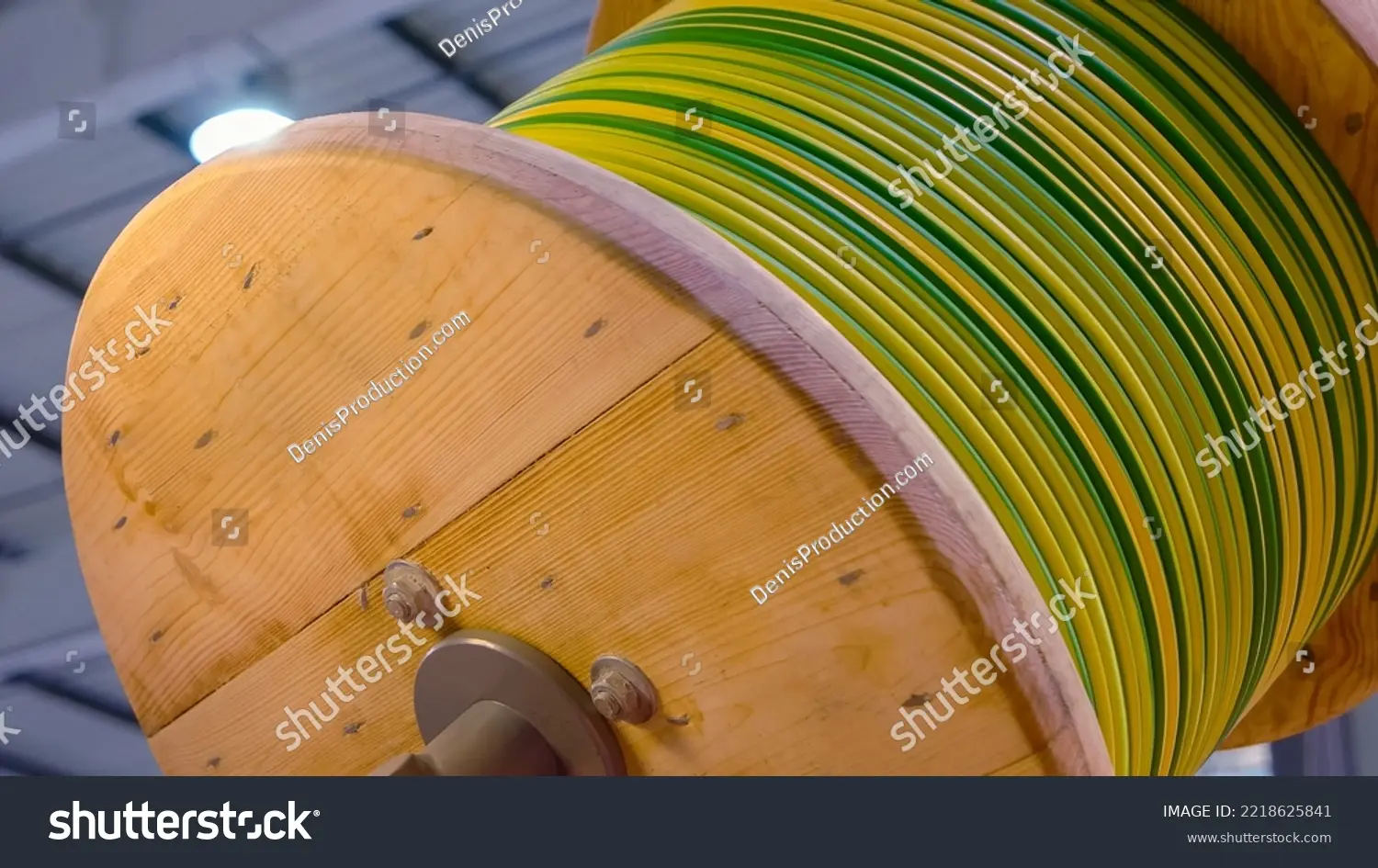
Wie Induktionserwärmung die Draht- und Kabelherstellung unterstützt
Induktionserwärmung bietet präzise, lokalisierte und energieeffiziente Wärme, die besonders für Inline- und Hochgeschwindigkeitsanwendungen geeignet ist. Sie wird zum Glühen, Vorwärmen, Trocknen, Aushärten und zur Oberflächenvorbereitung eingesetzt, verbessert Materialeigenschaften und sorgt für sauberere Prozesse.
Häufige Anwendungen der Induktionserwärmung in der Draht- und Kabelindustrie
- Ziel: Weichmachen des gezogenen Drahtes zur Wiederherstellung der Duktilität und Verringerung der Sprödigkeit
- Materialien: Kupfer, Aluminium, Edelstahl, Nickellegierungen
- Anwendungen:
- Elektrische Leiter
- Magnetdrähte
- Steuerkabel
- Vorteile:
- Gleichmäßiges und reproduzierbares Glühen bei hohen Produktionsgeschwindigkeiten
- Minimale Oxidation und Zunderbildung
- Einfache Integration in kontinuierliche Produktionslinien
- Ziel: Verbesserung der Haftung und Aushärteeffizienz von Beschichtungen oder Isolierungen
- Anwendungen:
- Extrusion von PVC oder Gummi
- Pulverbeschichtung
- Emalierung
- Vorteile:
- Erhöhte Beschichtungsuniformität
- Verbesserte Haftung
- Präzise Temperaturkontrolle zur Vermeidung von Verbrennungen
- Verwendet für:
- Beschichtungen (Epoxide, Farben, Emaille)
- Klebstoffschichten
- Schutz- oder Versiegelungsharze
- Vorteile:
- Schnelles und lokales Trocknen ohne Ofen
- Keine offene Flamme oder Verunreinigungen
- Energieeffizient und platzsparend
- Anwendungen:
- Drahtenden
- Abschirm- oder Erdungsverbindungen
- Vorteile:
- Saubere Verbindungen ohne Flussmittel
- Geeignet für Automatisierung und beengte Platzverhältnisse
- Verwendet für:
- Nitinoldrähte (medizinische oder spezielle Anwendungen)
- Spannungsabbau bei Hochspannungsanwendungen
- Vorteile:
- Präzise Temperaturkontrolle für spezifisches Materialverhalten
Vorteile der Induktionserwärmung in der Draht- und Kabelproduktion
- Inline-Kompatibilität: Ideal für kontinuierliche Produktion
- Energieeffizienz: Erwärmt nur das Produkt, nicht die Umgebung
- Kontaktlos und sauber: Verringert Kontaminationsrisiken
- Reproduzierbarkeit und Geschwindigkeit: Unterstützt enge Toleranzen und hohe Produktivität
- Kompakte Anlagen: Spart Platz gegenüber Öfen oder Trocknern
Kostenlose Probentests
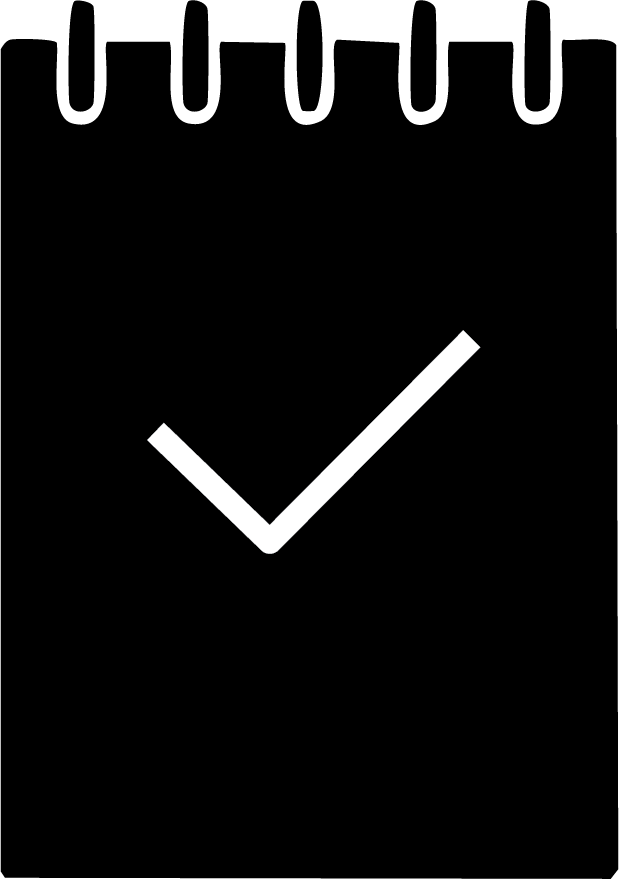
Schnelle Angebote
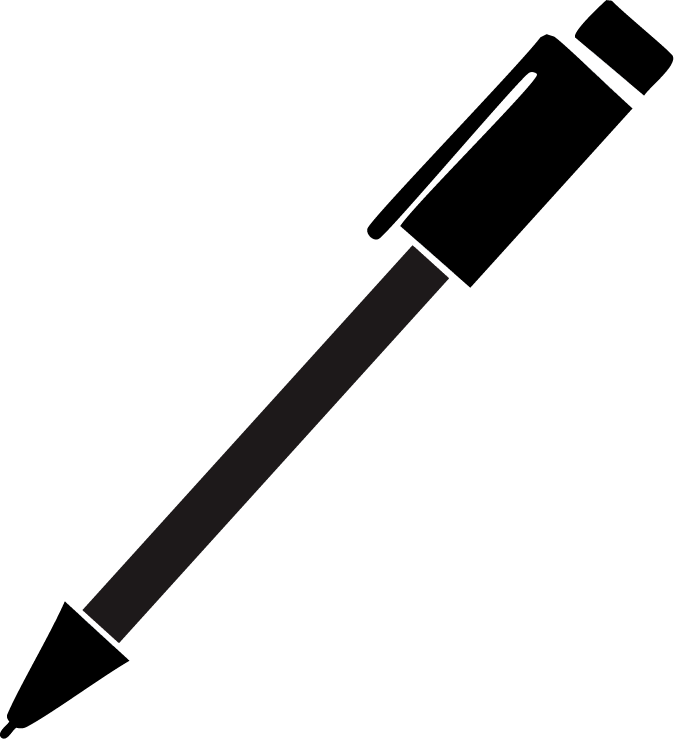